According to estimates in 2017 by the International Labour Organization (ILO), around 380,000 workers die from occupational accidents around the world every year. [Source: ILO]
Workers’ safety is of utmost importance in any environment but is absolutely critical when they are working in harsh and hazardous areas. Workers in these environments face added dangers and unpredictable conditions, which can put their safety in jeopardy in emergency situations, further exacerbated if they are in remote locations which have low connectivity and are hard to reach.
Positioning solutions were created to help companies oversee movements of their workers and ensure their safety, but existing systems face multiple environmental and connectivity challenges which means they have limited functionality, are expensive and are difficult to deploy.
What is a harsh environment?
Harsh environments generally refer to places with more extreme and challenging physical conditions.
For example:
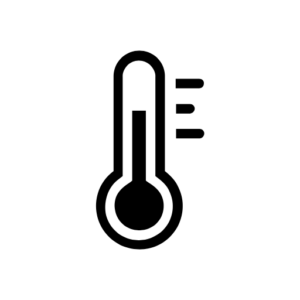
Extreme Temperatures
Extremely high or low temperatures – some components do not function out of a fixed temperature range.
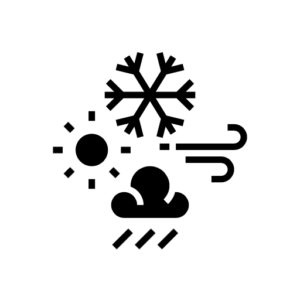
Changing Temperatures
Rapidly changing temperatures can cause thermal fatigue and mechanical stress. Large temperature ranges and fluctuations can cause components to work inconsistently
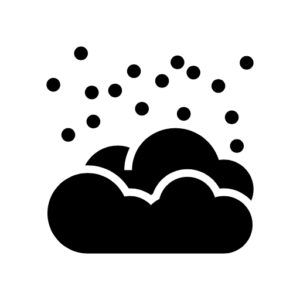
Dust
Accumulated dust in the environment reduces cooling ability and causes possible short circuits and fires.
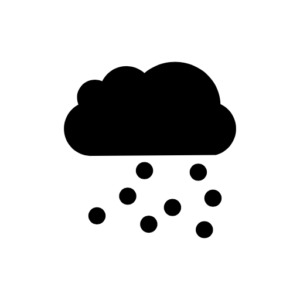
Precipitation
Rain, snow, ice, and sleet all have the potential to cause short circuits, while hail may also cause mechanical damage and shock
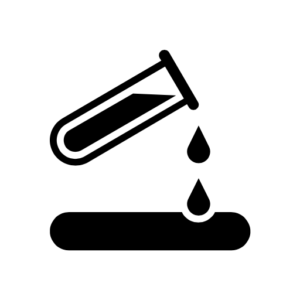
Corrosion
Sea spray and salt fogs corrode connectors, circuit boards and short circuit components when salt bridges from dried saltwater form, while Hydrogen Sulfide corrodes printed circuit boards
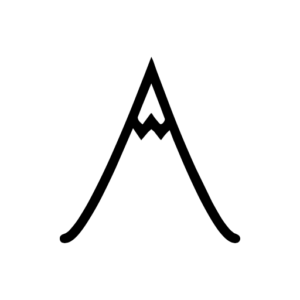
High Altitudes
Ambient atmosphere is less dense at altitude and reduces cooling ability, resulting in potential equipment overheating
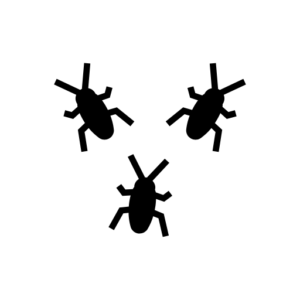
Animals and Insects
Electronics attracts nest and mound-building insects nests on equipment reduce cooling ability and may cause short circuits. Vermin may gnaw and destroy cables
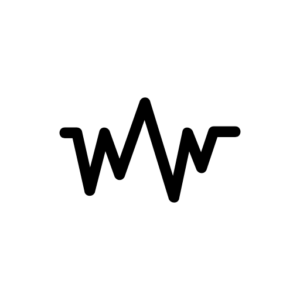
Vibration or Shock
Vibrations in moving machinery cause equipment fatigue resulting in mechanical and electrical failures. Physical shock can happen from sudden impact and collisions
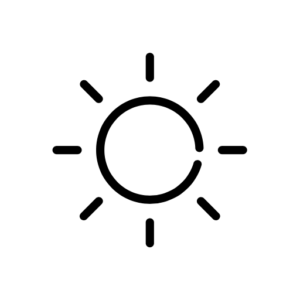
Exposure
Radiant heating from the sun causes equipment to overheat, while Ultraviolet light exposure can weaken materials over time
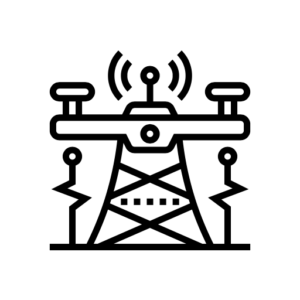
EMI
Electromagnetic Interference from nearby radio sources or welding equipment may cause unpredictable equipment operation or component failures
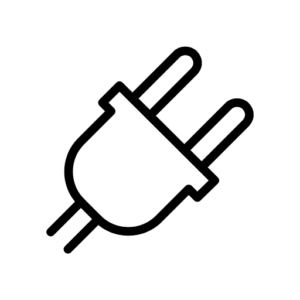
Noisy Electrical Power
Unfiltered and poorly regulated power from generators causes equipment stress and premature failure
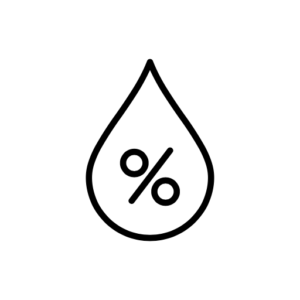
Humidity
High humidity can cause the alteration of component’s characteristics. Condensing humidity or condensation can cause short circuits.
Some common examples of harsh environments include:
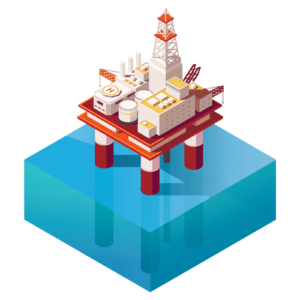
Oil and gas rigs
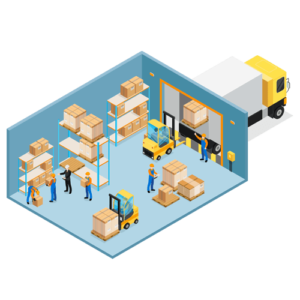
Industrial manufacturing plants
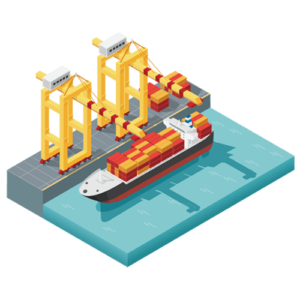
Container ships
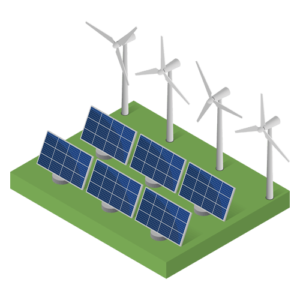
Wind farms
What is a hazardous environment?
Hazardous environments are more dangerous than harsh environments as these areas are potentially explosive.
Hazardous areas typically contain potentially ignitable concentrations of combustible substances like gases, vapors, dust or flyings, and when combined with ignition sources such as a hot surface on a running engine, an arcing wire, or even a discharge of static electricity create an explosion.
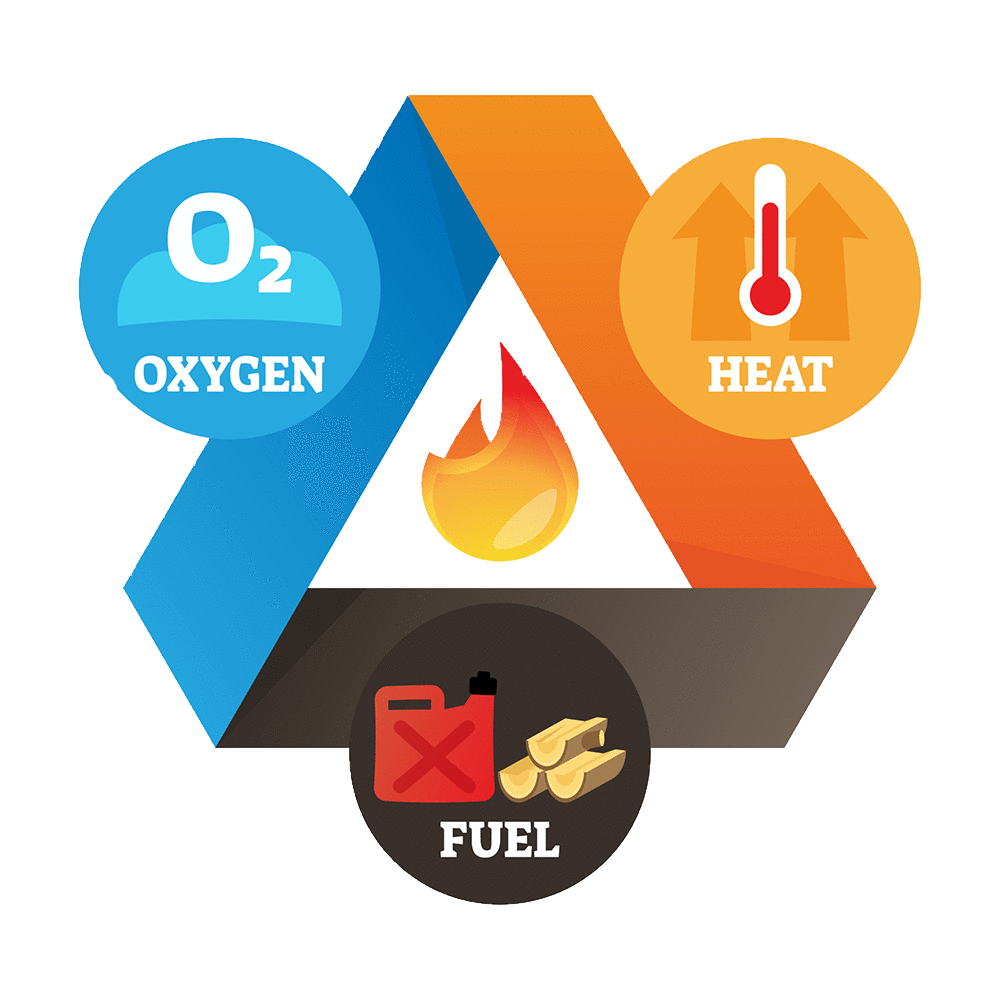
Some common hazardous industries include:
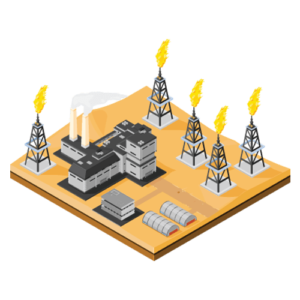
Petroleum / Oil and gas refineries / Drilling
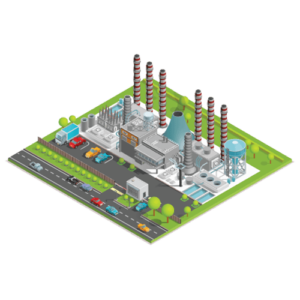
Specialty chemical / Cement / Paper / Plastic plants
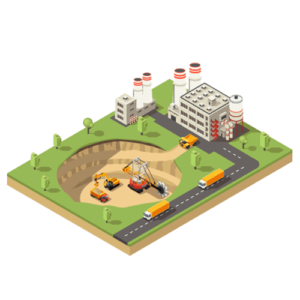
Mines
The European Union uses the Atmospheric Explosives Directive (ATEX) to regulate health and safety in hazardous areas and uses a zoning system to define how hazardous an area is through the frequency and duration of the occurrence of an explosive atmosphere:
[Source: EUR-Lex]
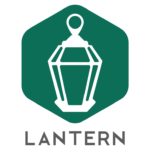
Lantern Positioning is a safety solution built for harsh and hazardous areas
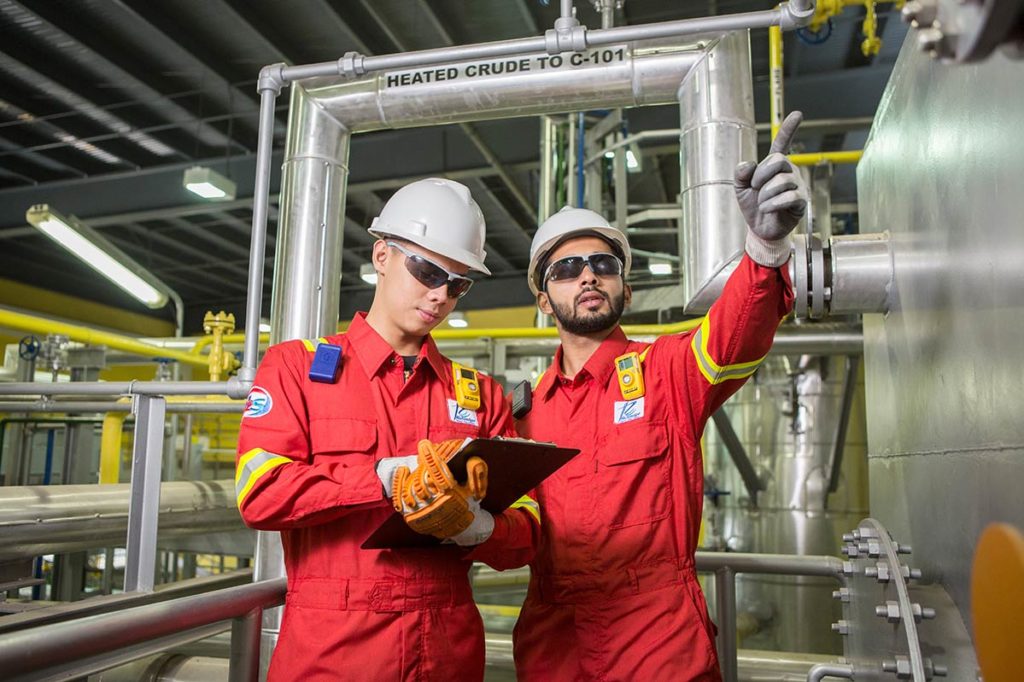
LanternEdge looked at the challenges faced by the industry in the creation of Lantern Positioning, a positioning solution designed to eliminate the inefficiencies and manual effort of current personnel management with near real time location of workers. This allows for the measuring and monitoring of worker’s locations as well as controlling deployment and worker occupancy, helping ensure the safety and productivity of workers.